Electroplating for Industry & Commerce
We offer precise electroplated coatings that meet the highest requirements. Our modern systems guarantee a long service life, effective corrosion protection and an attractive appearance for your products.
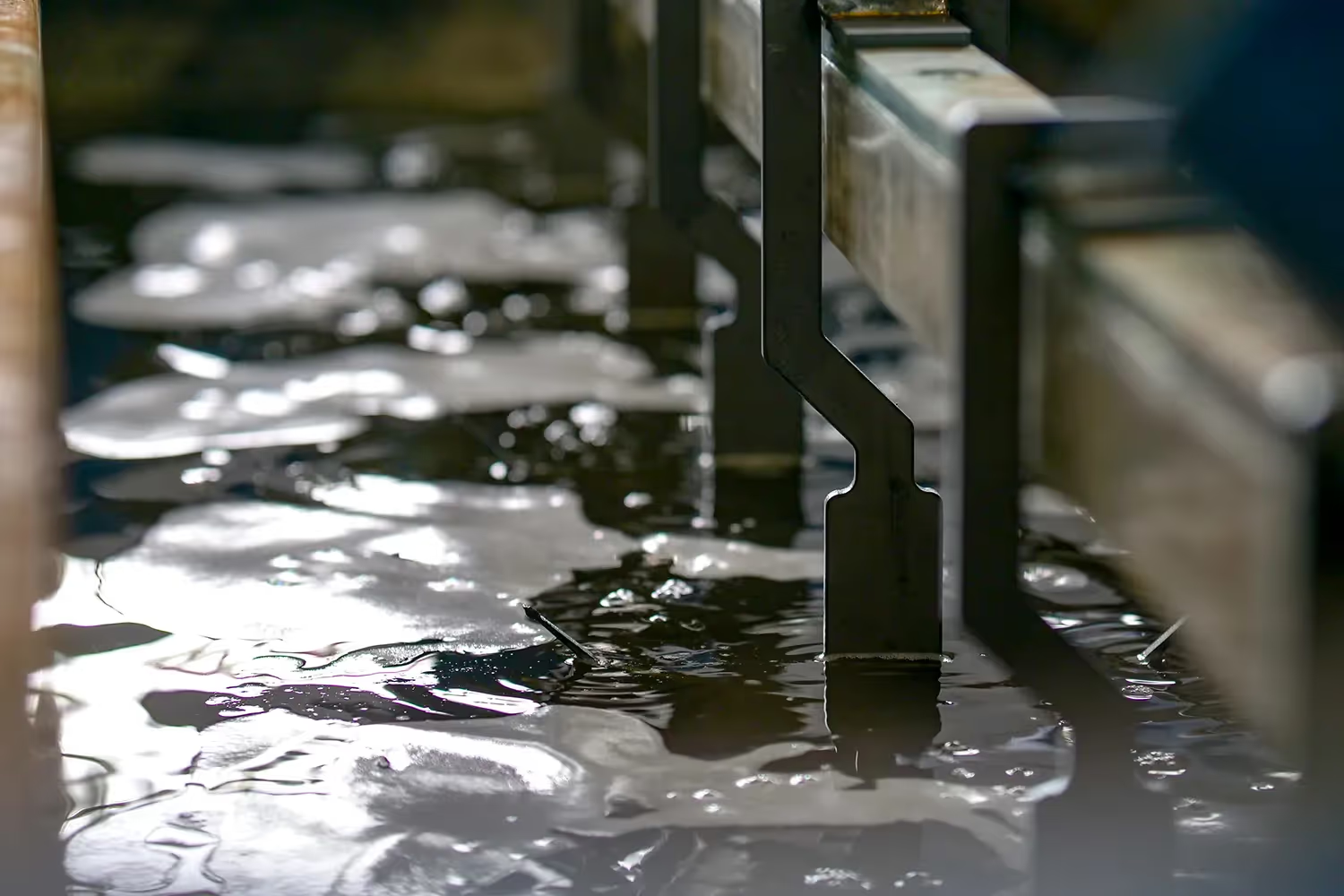
Electroplating Finishes for Increased Durability, Corrosion Resistance and Aesthetics
Tónus Kft. has a decades-long history of galvanizing metals.
The plant was commissioned in 2011 with two production lines, which have since been modernized to meet current needs and requirements.
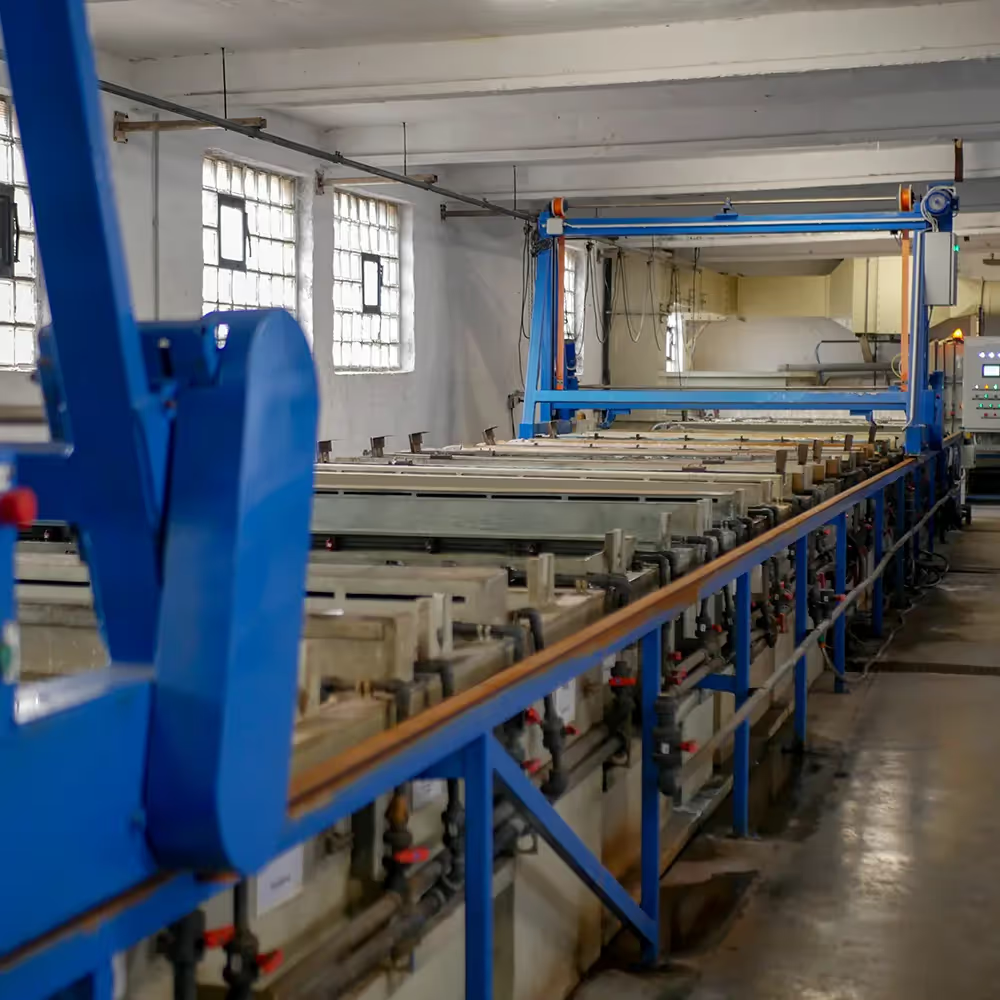
Our Electroplating Process
Preparation
The surface is thoroughly cleaned and prepared for the process.
Coating
The prepared surface is immersed in an electrolyte solution and connected to a power source.
Completion
The galvanized surface is tested and finished to achieve the desired appearance.
Your Supplier for High-Quality Electroplating Products
All Services From a Single Source
We are in close contact with the other areas of our company, which is necessary for the fast and precise production of our quality products.
High-Quality Materials
We source our materials from the German quality manufacturer Dr. Ing. Max Schlötter GmbH & Co KG (Geislingen) to guarantee our customers the best possible results.
Trained Staff
Our staff undergo regular training to ensure outstanding product quality and safety at the workplace.
Individual Offer
We also offer the galvanizing of individual products with zinc coating and prepare individual quotations for every type of workpiece.
Environmentally Friendly Production
We use state-of-the-art systems and processes to manufacture your products in an environmentally friendly manner and in compliance with legal requirements.
Punctuality & Reliability
We strive to meet our customers' requirements in every respect, both in terms of our surface treatment services and logistics.
High-Quality Electroplating Services You Can Trust
With the electroplating services of Tónus Kft., you benefit from our expertise, high-quality materials and state-of-the-art equipment. Our team of professionals has years of experience in providing exceptional electroplating solutions.
We use only the best materials and employ advanced techniques to ensure the highest level of quality and durability for your products. Our state-of-the-art equipment enables us to provide precise and efficient electroplating services that meet your specific requirements and exceed your expectations.
Our electroplating line is manually operated, which enables immediate and monitored intervention at all stages of the process, which also contributes to a higher surface quality.It also enables the simultaneous coating of different processed workpieces in the surface treatment line.
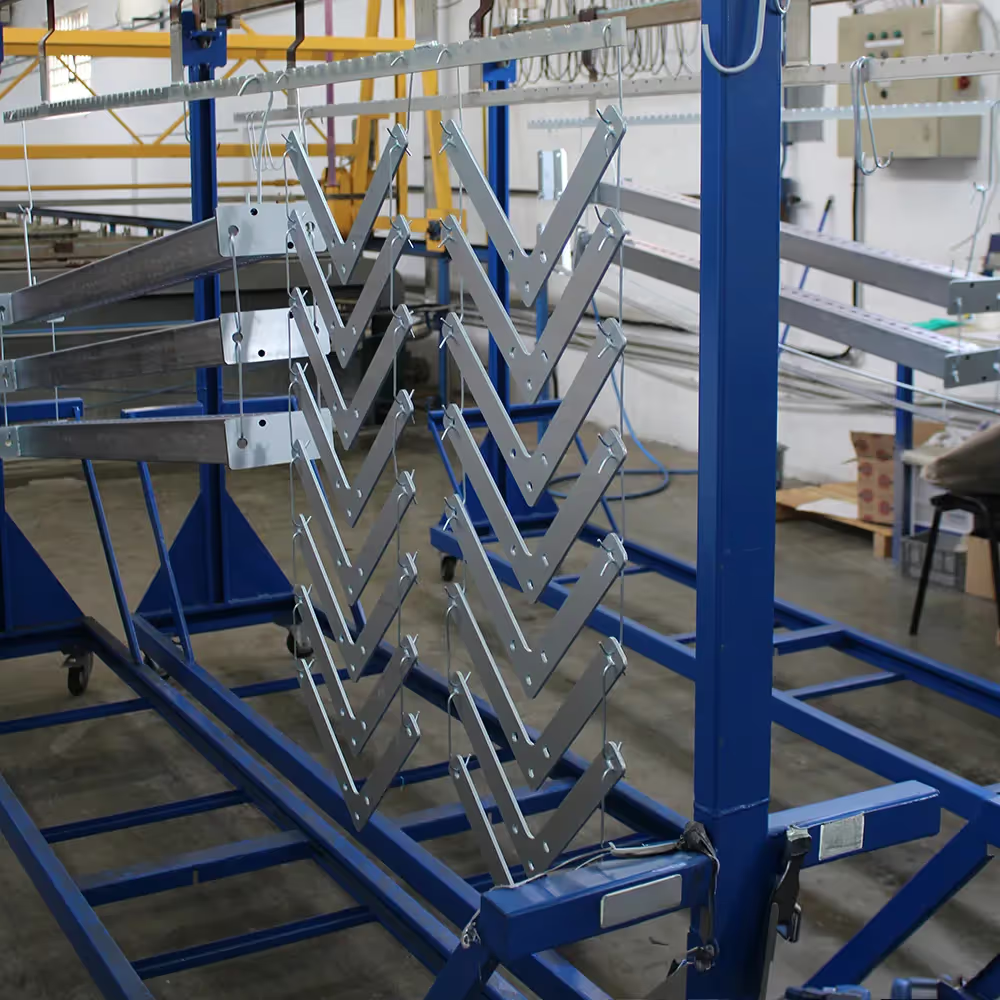
Inquire today and benefit from our experience!
We have been a partner to large commercial and industrial companies for more than 20 years. We look forward to welcoming you as a customer soon!
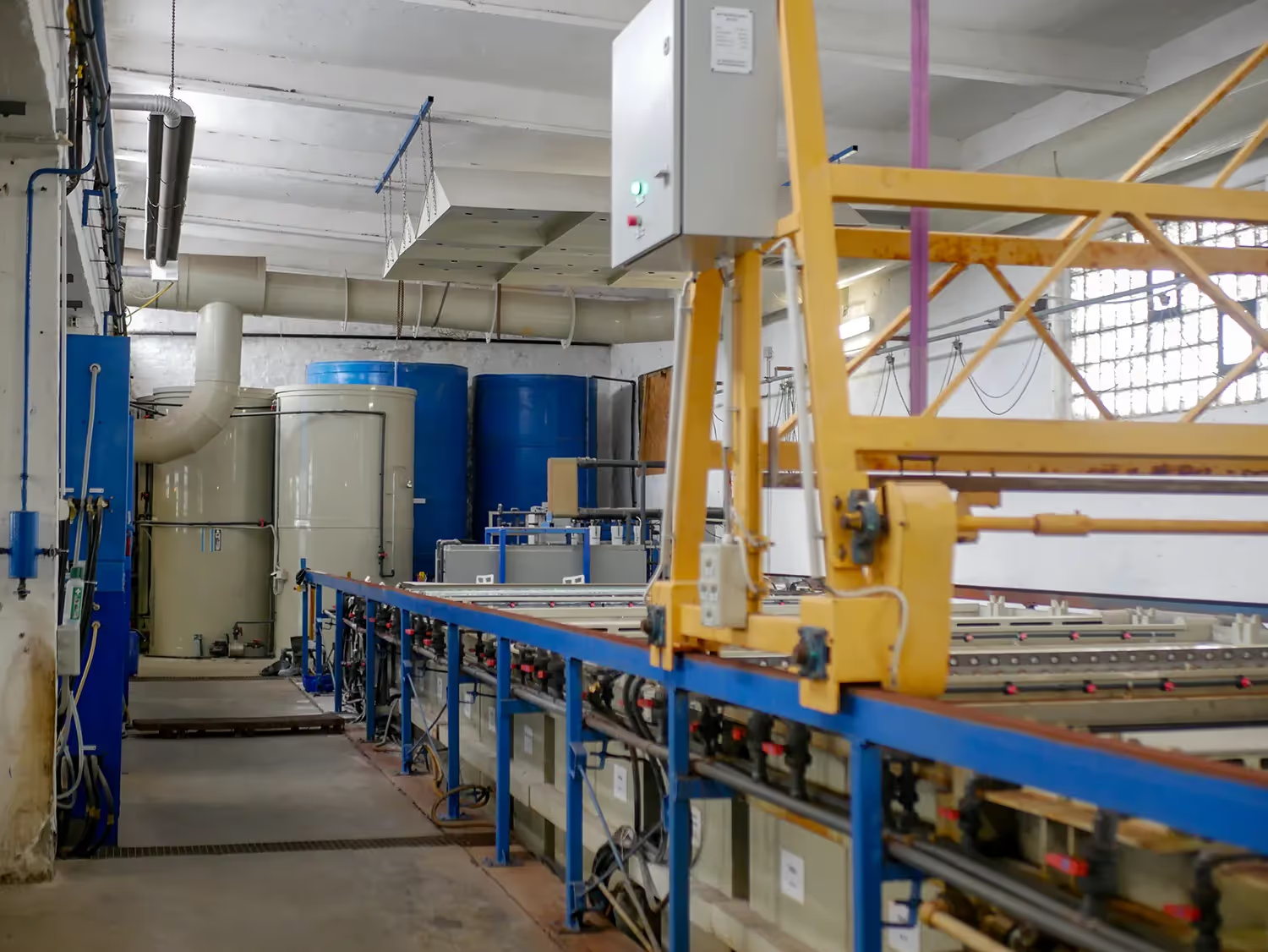
FAQs
Get answers to frequently asked questions about electroplating and learn more about Tónus Kft's expertise in this field.
What is electroplating?
Electroplating is an electrochemical process in which metals are coated using electrical currents. It is based on the principle of electrochemistry, in which chemical reactions are stimulated by electrical energy. The main components are an electrolyte solution, an anode (the coating material) and a cathode (the object to be coated). A power source provides the necessary voltage to enable the material to be transported.
This process is used to protect metals against corrosion, improve their adhesion or achieve a decorative finish. The chemical processes include the dissolution of metal ions at the anode and their deposition at the cathode.
(Source: Bard, A. J., & Faulkner, L. R. Electrochemical Methods: Fundamentals and Applications. Wiley, 2001).
What processes and techniques are used for electroplating?
There are various electroplating techniques that vary depending on the application. The most important processes include:
- Electroplating: Protection against rust.
- Nickel plating: Increasing wear resistance.
- Hard chrome plating: For mechanically stressed surfaces.
According to the Federal Institute for Materials Research and Testing (BAM), 2022. there is a significant difference between electrolytic deposition, in which an electric current is used, and electroless plating, which is based on chemical reactions. Modern alternatives such as powder coating or anodizing offer additional options for specific applications.
What preparation techniques are used before electroplating?
The quality of the electroplated coating depends largely on the preparation of the surface. The most important steps include:
- Mechanical grinding and polishing: Unevenness is removed.
- Chemical cleaning and degreasing: Impurities are removed.
- Adhesion tests: Ensuring that the coating adheres optimally.
What materials and chemicals are used for electroplating?
Metals such as zinc, nickel, chrome and gold are used for electroplating. Their selection depends on the desired properties, such as corrosion protection or conductivity.
Electrolytes containing metal salts and additives play a central role in the process. However, handling chemicals such as cyanide solutions requires special precautions as they are harmful to health. According to Schlesinger, M. & Paunovic, M. Modern Electroplating, more environmentally friendly alternatives such as sulphate-based electrolytes are increasingly being explored. Wiley, 2010. increasingly being researched.
What are the advantages of electroplating?
Electroplating extends the service life of metal products by creating a robust protective layer. It makes the material more resistant to corrosion and at the same time ensures a visually appealing, uniform surface finish.
How does electroplating work in metal technology?
We only carry out suspended surface treatments in our plant. This process ensures a uniform and high-quality coating.
The process begins with a thorough pre-treatment. Chemical and electrochemical degreasing removes oily residues and other impurities from the surface. The surface is then activated to make it metal-free and surface-active. This creates the ideal basis for a high-quality metal coating.
A zinc anode serves as the material source for the coating process, while the surface to be coated acts as the cathode. The cathode is immersed in a zinc bath, which is equipped with a vertical cathode movement. This movement ensures an even coating of the workpiece.
The electrolysis process is started by using direct current. This forms a corrosion-resistant metallic coating on the steel part. The coating thickness varies between 8 and 20 µm, depending on the customer's specific requirements.
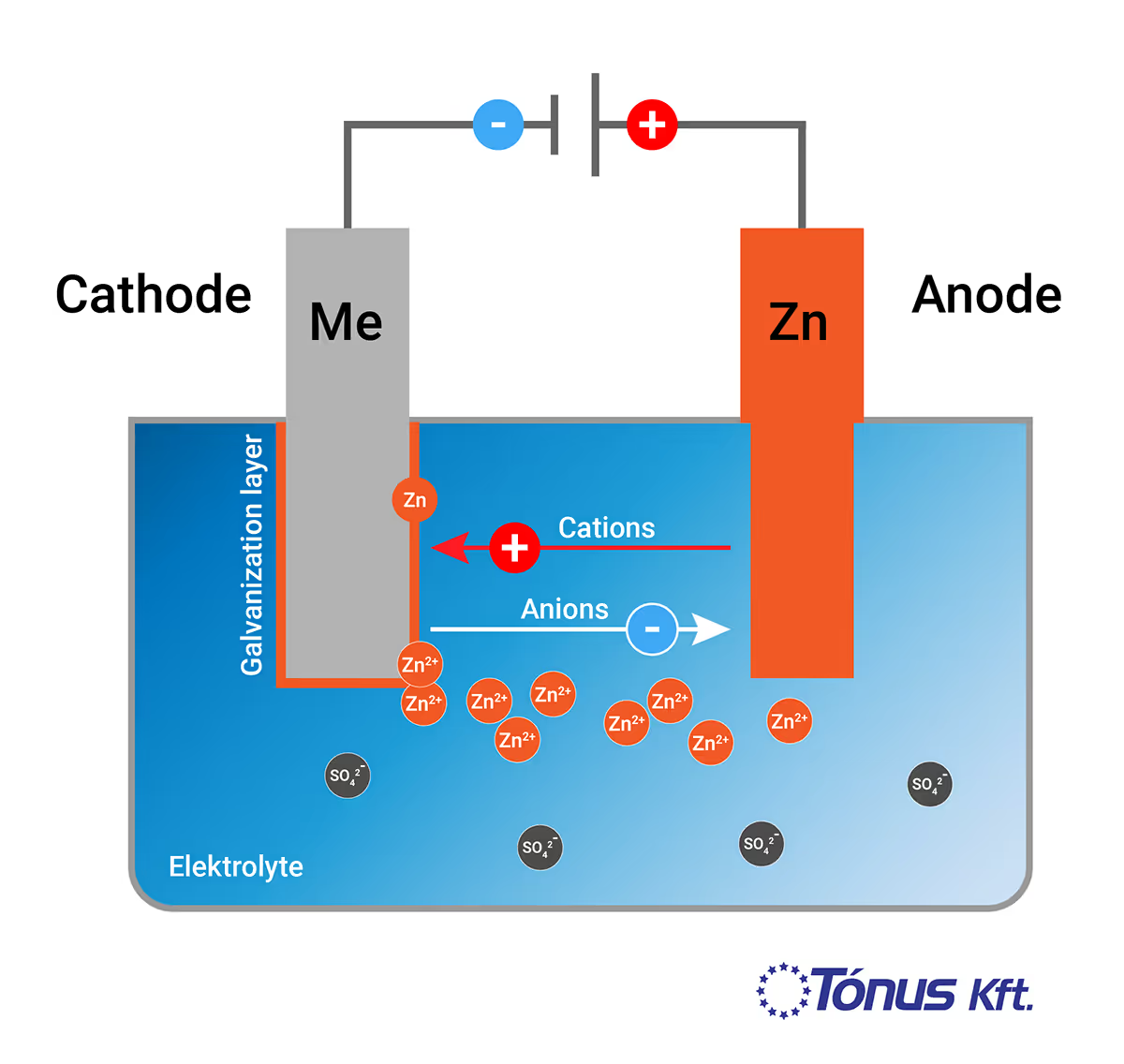
After coating, the surface is treated with corrosion-resistant passivation solutions. Depending on the customer's requirements, we use blue or yellow passivations, which provide additional protection and a high-quality appearance.
Nach der Oberflächenbehandlung benötigen die Werkstücke keinen weiteren Oberflächenschutz, können aber auf Wunsch lackiert werden, was auch im Haus möglich ist.
Which materials can be electroplated?
We galvanize workpieces made of steel, wrought iron, cast iron and copper.
What different manufacturing processes does Tónus Kft. offer in electroplating?
Tónus Kft. carries out surface treatment in two production lines, which allow different maximum workpiece dimensions and post-treatment options:
- Line I
Maximum workpiece size: 2000 x 850 x 450 mm
Post-treatment: blue or yellow passivation - Line II
Maximum workpiece size: 2800 x 1100 x 550 mm
Post-treatment: Blue passivation
This configuration enables precise and high-quality processing of workpieces in various sizes.
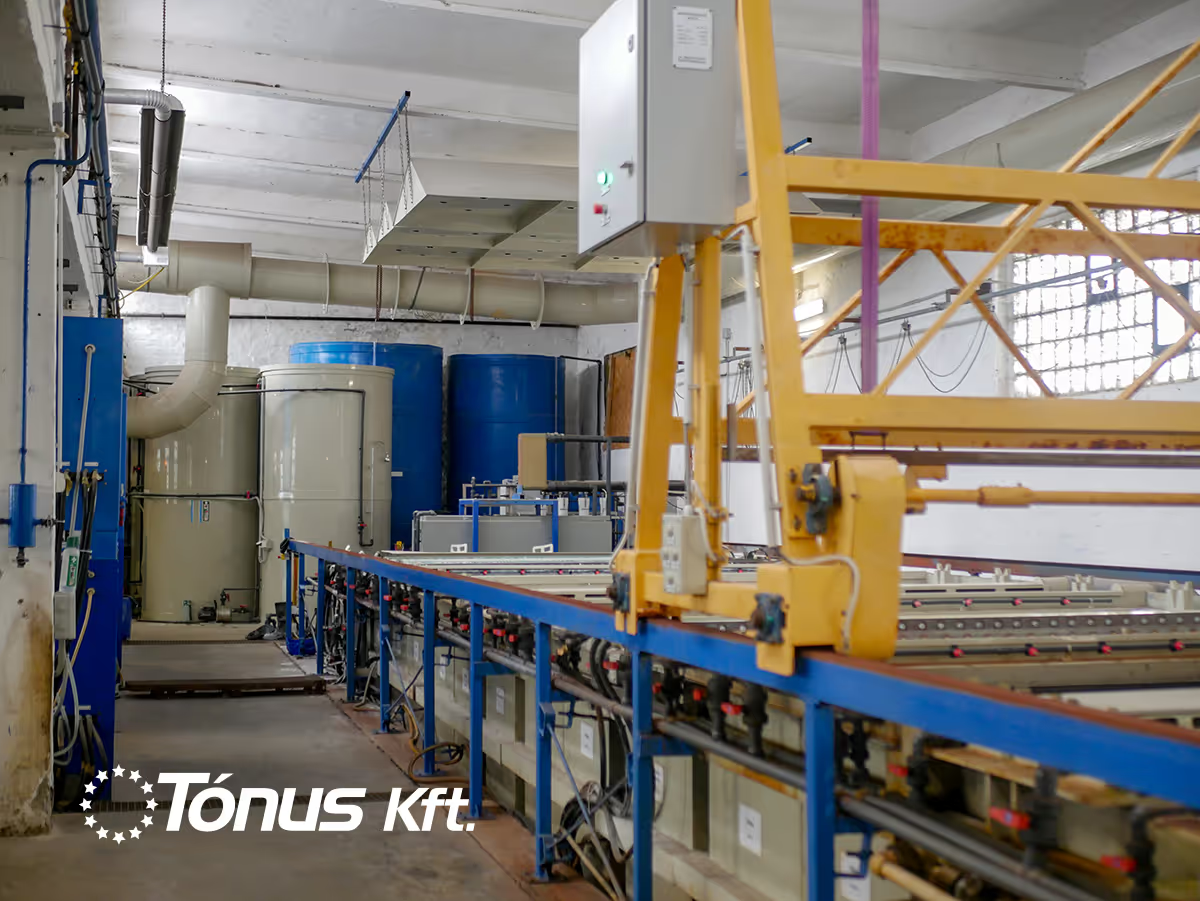
How much does it cost to electroplate metals?
The cost of electroplating depends on the specific requirements of the end product, such as the desired coating thickness, workpiece dimensions and post-treatment. Our team will be happy to provide you with an individual quote that is tailored precisely to your needs.
What impact does electroplating have on the environment?
The technology used is modern, environmentally friendly and meets today's needs and requirements.
- Recycling metal waste: Reducing material consumption
- Emission control: modern filter technologies minimize harmful emissions
We operate under a comprehensive environmental permit and use the best available techniques for the surface treatment of metals.
The technology used is modern, environmentally friendly and meets today's needs and requirements.
The passivation is Cr(VI)-free.
What layer thickness is achieved during electroplating?
During electroplating, a coating with a thickness of up to 20 µm can be applied. The exact thickness is adapted to the customer's requirements.
In which industries is electroplating of products used particularly frequently?
- Construction and building materials industry
- Automotive industry
- Electronics industry
- Jewelry industry
- Household appliance industry
- Aerospace industry
- Packaging industry
- Heavy industry
- Medical equipment industry
Special processes even make it possible to coat plastics, which is relevant in the automotive and household appliance industries.
How does quality assurance take place during electroplating?
In order to be able to offer our customers the highest possible product quality, we continuously implement quality assurance measures. These measures include:
- Inspection of finished products
- Coating thickness measurements (ensures uniform coatings)
- Surface inspection (identifies defects such as cracks or pores)
- Long-term tests (check durability under real conditions)
- Porosity tests
- Salt spray test
- Chemical composition testing
- Electrical tests (if required)
- Documentation and records
- Accurate process controls
- Ongoing training and qualification of our personnel
- Error analyses